What Advancements In Technology Are Used In Reconditioning Jaguar Engines?
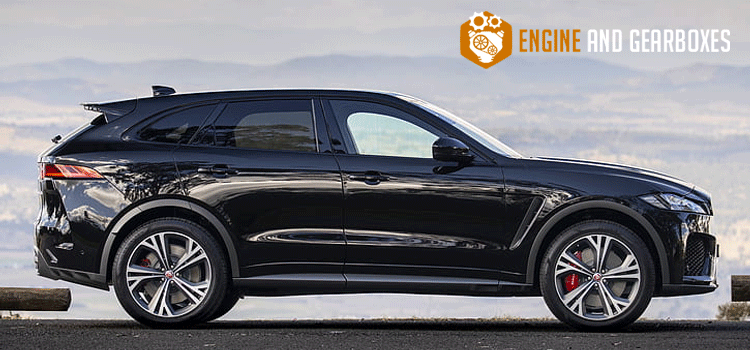
The reconditioning of Jaguar engines is a complex and highly specialized process that has seen significant technological advancements in recent years. These advancements have revolutionized the way reconditioned engines are prepared, ensuring they deliver performance that is as close to new as possible. From precision machining to advanced diagnostics, the reconditioning industry has embraced cutting-edge technology to meet the high standards expected by Jaguar owners.
We delves into the latest technological innovations that are used in reconditioning Jaguar engines, with a focus on how these advancements improve engine reliability, performance, and longevity. Additionally, we’ll discuss the importance of choosing the right service provider for engine replacement, reconditioned engines, and supply and fit services.
Precision Machining and Surface Finishing
One of the key advancements in reconditioning Jaguar engines is the use of precision machining and surface finishing techniques. Modern CNC (Computer Numerical Control) machines are capable of machining engine components to incredibly tight tolerances, ensuring that all parts fit together perfectly. This precision is critical in maintaining the performance characteristics of the original engine.
Surface finishing techniques, such as micro-polishing, are also used to reduce friction between moving parts, thereby increasing the engine’s efficiency and lifespan. This process involves smoothing the surfaces of components like crankshafts and camshafts to a mirror-like finish, which reduces wear and tear. These technological advancements in machining and finishing ensure that reconditioned engines not only perform like new but also have a prolonged operational life, making them a cost-effective option for Jaguar owners seeking engine replacement solutions.
Advanced Diagnostic Tools
The use of advanced diagnostic tools is another significant technological advancement in the reconditioning of Jaguar engines. Modern diagnostic equipment allows technicians to identify issues with engine components with a high degree of accuracy. This includes checking for problems that may not be immediately visible, such as internal cracks or wear that could lead to future failures.
These tools use techniques such as ultrasonic testing, X-ray imaging, and 3D scanning to thoroughly inspect every component of the engine. By identifying and addressing potential issues during the reconditioning process, these advanced diagnostics help ensure that the reconditioned engines meet or exceed the performance standards of new engines. For customers seeking engine replacement or reconditioned engines, this level of thoroughness provides peace of mind, knowing that the engine has been fully inspected and is free from defects.
Enhanced Material Science and Coatings
Recent advancements in material science and coatings have played a pivotal role in the reconditioning of Jaguar engines. The development of stronger, more durable materials has improved the longevity and reliability of reconditioned engines. For instance, the use of advanced alloys and composite materials in engine components helps to withstand higher temperatures and stresses, which are common in high-performance engines like those found in Jaguars.
Additionally, the application of advanced coatings, such as ceramic coatings, to engine parts has enhanced their performance. These coatings reduce heat and friction, leading to improved engine efficiency and reduced wear. By incorporating these materials and coatings into the reconditioning process, engine rebuilders can deliver reconditioned engines that offer superior durability and performance, making them a viable option for engine replacement or supply and fit services.
Computer-Aided Design (CAD) and Simulation
Computer-Aided Design (CAD) and simulation technologies have become indispensable in the reconditioning process of Jaguar engines. These tools allow engineers to design and test engine components virtually before they are manufactured. By simulating various operating conditions, engineers can identify potential weaknesses or areas for improvement in the engine’s design.
This technology ensures that reconditioned engines are not just copies of the original but are optimized for better performance and efficiency. The use of CAD and simulation also speeds up the reconditioning process, as potential issues can be addressed before the actual rebuilding begins. For Jaguar owners seeking reconditioned engines, this means getting an engine that has been fine-tuned for optimal performance, often exceeding the capabilities of the original engine.
Laser Technology for Component Restoration
Laser technology has emerged as a powerful tool in the reconditioning of Jaguar engines, particularly in the restoration of engine components. Laser cladding, for instance, is a process where a laser is used to melt and bond material onto the surface of a worn component. This technique is used to restore parts such as crankshafts, camshafts, and valve seats to their original specifications.
The precision of laser technology ensures that the restored components meet or exceed the original manufacturing standards. This level of accuracy is crucial in high-performance engines, where even the smallest deviation can impact performance. By using laser technology, engine reconditioners can restore parts that would otherwise need to be replaced, reducing costs and ensuring that reconditioned engines are as good as new. This advancement is particularly beneficial for Jaguar owners looking for cost-effective engine replacement options.
Additive Manufacturing (3D Printing)
Additive manufacturing, commonly known as 3D printing, has made significant inroads into the reconditioning of Jaguar engines. This technology allows for the production of complex engine components that are difficult or impossible to manufacture using traditional methods. 3D printing is particularly useful in producing parts that are no longer available or are custom-designed for specific engine models.
The ability to produce parts on-demand using 3D printing reduces lead times and ensures that reconditioned engines can be completed more quickly. Moreover, the materials used in 3D printing are often lighter and stronger than traditional materials, leading to improved engine performance. For those in need of reconditioned engines or supply and fit services, the incorporation of 3D printed components ensures that the reconditioned engine is both reliable and efficient.
Automated Assembly and Testing
Automation has revolutionized the assembly and testing phases of the reconditioning process. Automated assembly lines ensure that engine components are assembled with high precision and consistency. This reduces the likelihood of human error, which can lead to performance issues in the reconditioned engine.
Automated testing rigs are also used to simulate real-world operating conditions, ensuring that the reconditioned engine performs to the required standards. These rigs can test various aspects of the engine, such as compression, fuel efficiency, and emissions, under different load conditions. The use of automation in assembly and testing guarantees that reconditioned engines meet the same stringent quality standards as new engines, making them a reliable choice for engine replacement.
Data Analytics and Machine Learning
Data analytics and machine learning are the latest technological advancements being used in the reconditioning of Jaguar engines. By analyzing vast amounts of data collected from previous reconditioning projects, machine learning algorithms can predict potential issues and recommend optimal solutions. This data-driven approach allows for more precise reconditioning, as patterns and trends in engine performance can be identified and addressed.
Machine learning is also used to optimize the reconditioning process itself, improving efficiency and reducing costs. For Jaguar owners seeking reconditioned engines, this means receiving an engine that has been rebuilt using the most advanced techniques available, ensuring top performance and reliability. The integration of data analytics into the reconditioning process also allows for continuous improvement, as insights from each project contribute to better outcomes in the future.